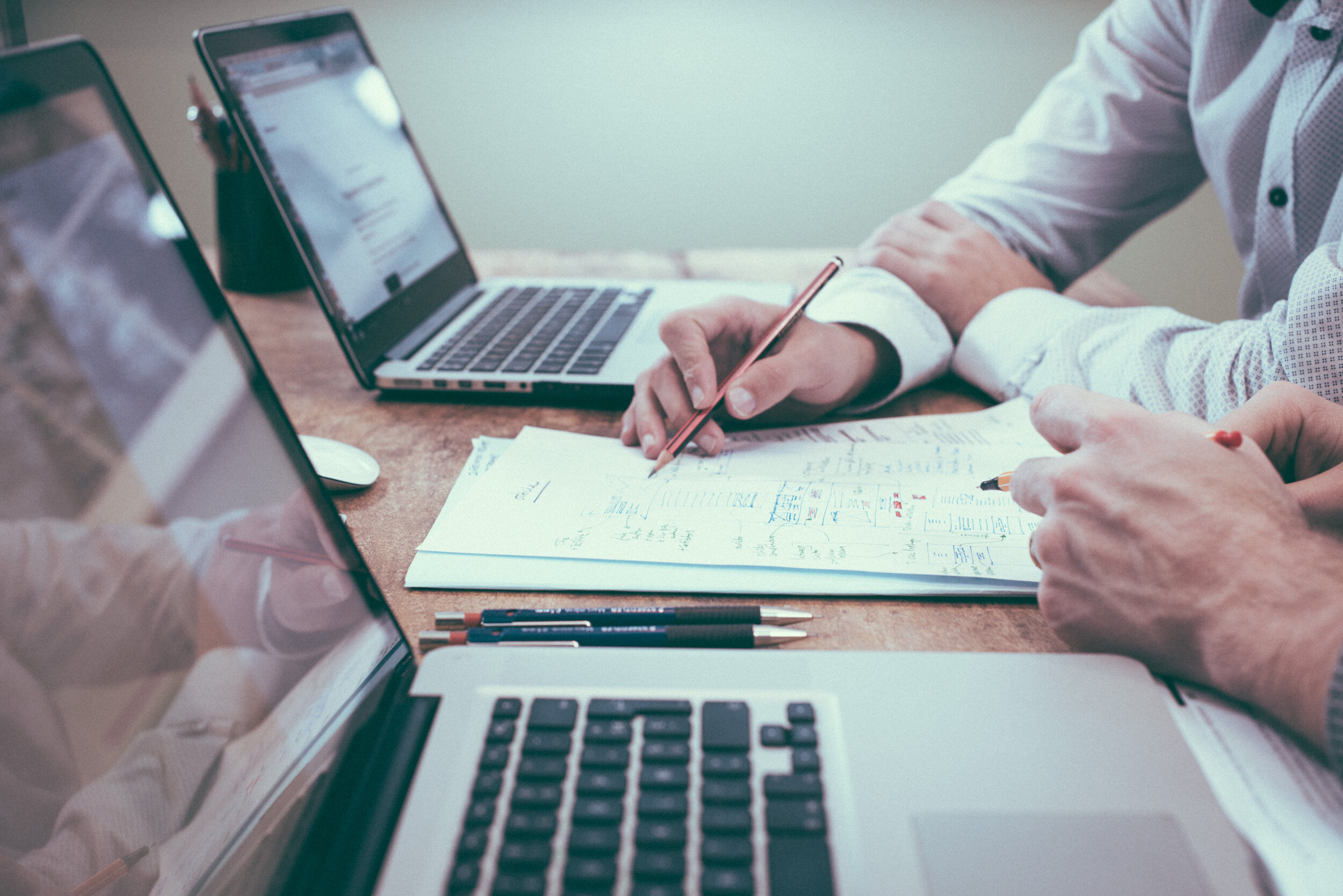
Research Center of Materials & Coatings
The Harber Coatings research centre provides scientific and engineering consulting services for industrial materials and optimal coating practices. We generate advantageous solutions for equipment optimization and empower users with leading knowledge on how to economically invest in and protect valuable company assets to minimize maintenance and/or replacement costs, as well as significantly reduce downtime due to equipment failure. Our research centre provides:
Material and coating selection proposals based on proven academic results transferred into industrial applications.
Material testing methodology studies and interpretation of collected test data result properties.
Up-to-date material and coating selection case studies vs. different industrial applications with detailed technical data base. Data is not open to the public, and only includes information collected under legal permission. Client’s information shall never be disclosed.
Material failure mode study and material failure predictability study.
Coating failure mode study and coating failure predictability study.
Large scale/massive scale coating production quality control.
Large/massive part coating inspection procedures.
Material and coating selection – analysis on engineering, feasibility and economy.
Advanced material, coating and coating process studies.
Selective co-operations partnerships with academic research institutes.
Proper Material And Coating Selection
In general, material assessment falls in two areas – academic/lab assessment, and engineering assessment. The former focuses on the study of material nature, the latter focuses on how to pick ideal material and coating pairing (when coating is required) based on known material nature and the application environment it will be exposed to.
Different materials are selected and used for various purposes based on the product design, desired longevity, material performance, material availability, affordability and long-term maintenance cost. Material selection, preventative maintenance, periodic inspection, emergency inspection, repair/maintenance, and replacement are usually practiced as routine work. We work with users to develop strategies to decrease these economic pain points and achieve a competitive advantage, to increase equipment performance and reliability.
Material Failure Is Predictable
Corrosion, erosion and aging are the major factors for material and coating failure. Failure can occur with proper design (along with time) or with under design, due to improper material selection and/or coating deficiency. Dealing with such failures has become routine maintenance work, yet is often preventable.
Corrosion, erosion and/or some kind of aging usually starts at the surface of the material. Properly functioning coatings will effectively protect substrate materials to achieve exceptional working longevity and greatly increase equipment reliability. If the material is either “over-qualified” and excessive for the project’s function, or insufficient in quality for the specific application, the selection of material and/or coating is incorrect for that project.
Often, unexpected coating failures frustrate users. In certain cases users would rather select expensive material for perceived predictability, without having the best performance and economic value. Proper material and coating pairing can allow a much less expensive substrate material to be used and still greatly outperform expensive raw material. Therefore, scientific assessment of material, and coating selection (if coating is required), is extremely important for users. The appropriate selection of materials and coatings will let companies spend their budget in the most effective manner for specific needs and prevent unnecessary spending.
Effective coatings which surface engineer substrate materials, not only provide surface protection but, can also provide superior surface hardness and surface lubrication, per the design. Effective surface engineering is the key to significantly reducing corrosion and wear damage, ultimately resulting in substantial cost savings.